項目概述
1. 生產計劃
600套/天(117/118軸承座)
2. 加工線要求:
1)適用於自動生產線的CNC加工中心;
2)液壓工裝夾具;
3)自動上下料裝置及輸送裝置;
4)總體加工製程及加工週期;
生產線佈局
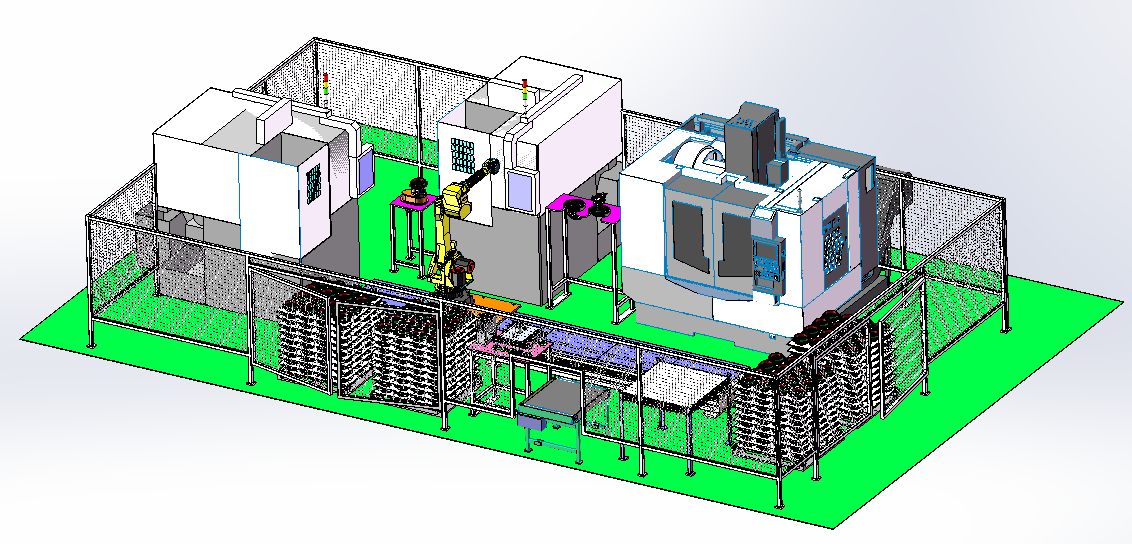
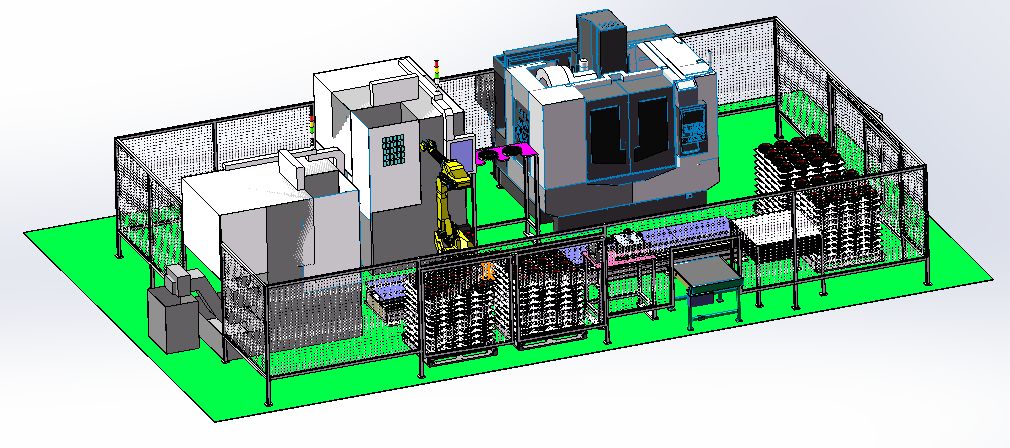
生產線佈局
機器人動作介紹:
1、將粗加工、擺放好的籃子手動放置在載物台上(1號載物台、2號載物台),並按鍵確認;
2.機器人移動到1號上料台的托盤處,打開視覺系統,抓取A、B零件並分別移動到角度觀察站等待上料指令;
3.角度辨識工位發出上料指令,機器人將1號工件放入轉盤定位區域,轉動轉盤並啟動角度辨識系統,確定角度位置,停止轉盤,完成1號工件的角度辨識;
4.角度辨識系統發出下料指令,機器人拿起1號工件,放入2號工件辨識。轉盤旋轉,角度辨識系統啟動確定角度位置。轉盤停止,2號工件角度辨識完成,發出下料指令;
5.機器人接收1號立車下料指令,運動至1號立車上下料位進行下料上料,此動作完成後,立車單件加工循環開始;
6.機器人將1號立車加工完畢的成品取走,放置到工件翻轉台1號位置;
7.機械手接收到2號立車下料指令,運動至2號立車上下料位進行下料上料,完成動作,開始立車單件加工循環;
8.機器人將2號立車加工完畢的成品取走,放置到工件翻轉台的2號位置;
9、機器人等待立式加工的下料命令;
10.立式加工發出下料指令,機器人運動至立式加工上下料位,分別抓取並移動1號、2號工位的工件至下料托盤上,並將工件分別放置於托盤上;機器人運動至翻轉台,分別抓取並送入1號、2號工位至立式加工上下料位,並將1號、2號機器人移出立式加工安全距離,開始單次加工循環;
11.機器人運動至1號載料盤,準備啟動二次循環程序;
描述:
1.機器人取料托盤上的16件(一層),機器人將吸盤夾鉗更換,並將隔板放入暫存籃內;
2.機器人將16件(一層)裝在下料托盤上,機器人要更換一次吸盤鉗,將隔板放在從暫存籃中取出的零件的隔間面上;
3.根據檢查頻率,確保機器人將零件放置在手動取樣台上;
1 | 加工週期時間表 | ||||||||||||||
2 | 顧客 | 工件材料 | QT450-10-GB/T1348 | 工具機型號 | 檔案編號 | ||||||||||
3 | 產品名稱 | 117 軸承座 | 圖號 | DZ90129320117 | 準備日期 | 2020.01.04 | 編制 | ||||||||
4 | 工藝步驟 | 刀號 | 加工內容 | 工具名稱 | 切割直徑 | 切割速度 | 轉速 | 每轉進給 | 工具機進給 | 扦插次數 | 每個工序 | 加工時間 | 空閒時間 | 四軸旋轉時間 | 換刀時間 |
5 | 不。 | 不。 | 解說 | 工具 | D 毫米 | n | 轉速 | 毫米/轉 | 毫米/分鐘 | 時代 | mm | 秒 | 秒 | 秒 | |
6 | ![]() | ||||||||||||||
7 | 1 | T01 | 銑削安裝孔表面 | 40面銑刀直徑 | 40.00 | 180 | 1433 | 1.00 | 1433 | 8 | 40.0 | 13.40 | 8 | 4 | |
8 | 鑽直徑 17 的安裝孔 | 直徑17組合鑽 | 17.00 | 100 | 1873 | 0.25 | 468 | 8 | 32.0 | 32.80 | 8 | 4 | |||
9 | T03 | DIA17孔背倒角 | 反向倒角刀 | 16.00 | 150 | 2986 | 0.30 | 896 | 8 | 30.0 | 16.08 | 16 | 4 | ||
10 | 描述: | 切割時間: | 62 | 第二 | 夾具裝夾及上料下料時間: | 30.00 | 第二 | ||||||||
11 | 輔助時間: | 44 | 第二 | 總加工工時: | 136.27 | 第二 |
1 | 加工週期時間表 | |||||||||||||||||
2 | 顧客 | 工件材料 | QT450-10-GB/T1348 | 工具機型號 | 檔案編號 | |||||||||||||
3 | 產品名稱 | 118軸承座 | 圖號 | DZ90129320118 | 準備日期 | 2020.01.04 | 編制 | |||||||||||
4 | 工藝步驟 | 刀號 | 加工內容 | 工具名稱 | 切割直徑 | 切割速度 | 轉速 | 每轉進給 | 工具機進給 | 扦插次數 | 每個工序 | 加工時間 | 空閒時間 | 四軸旋轉時間 | 換刀時間 | |||
5 | 不。 | 不。 | 解說 | 工具 | D 毫米 | n | 轉速 | 毫米/轉 | 毫米/分鐘 | 時代 | mm | 秒 | 秒 | 秒 | ||||
6 | ![]() | |||||||||||||||||
7 | 1 | T01 | 銑削安裝孔表面 | 40面銑刀直徑 | 40.00 | 180 | 1433 | 1.00 | 1433 | 8 | 40.0 | 13.40 | 8 | 4 | ||||
8 | T02 | 鑽直徑 17 的安裝孔 | 直徑17組合鑽 | 17.00 | 100 | 1873 | 0.25 | 468 | 8 | 32.0 | 32.80 | 8 | 4 | |||||
9 | T03 | DIA17孔背倒角 | 反向倒角刀 | 16.00 | 150 | 2986 | 0.30 | 896 | 8 | 30.0 | 16.08 | 16 | 4 | |||||
10 | 描述: | 切割時間: | 62 | 第二 | 夾具裝夾及上料下料時間: | 30.00 | 第二 | |||||||||||
11 | 輔助時間: | 44 | 第二 | 總加工工時: | 136.27 | 第二 | ||||||||||||
12 |
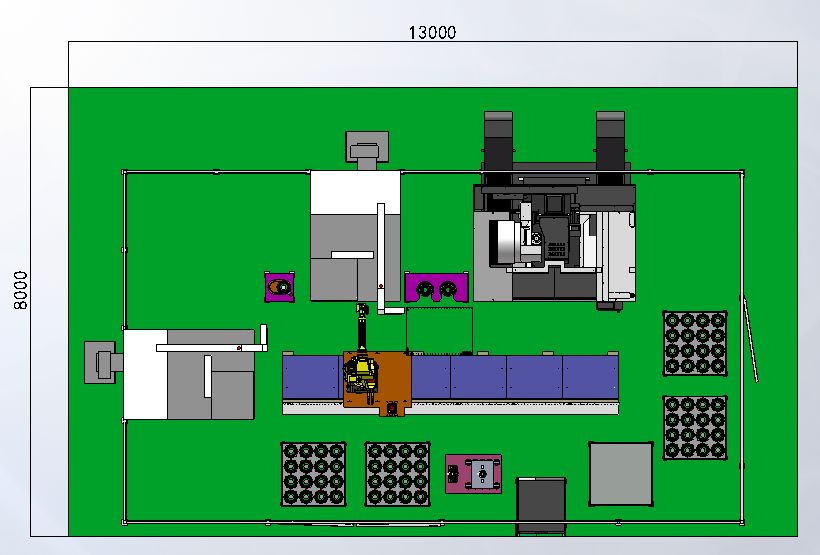
生產線覆蓋面積
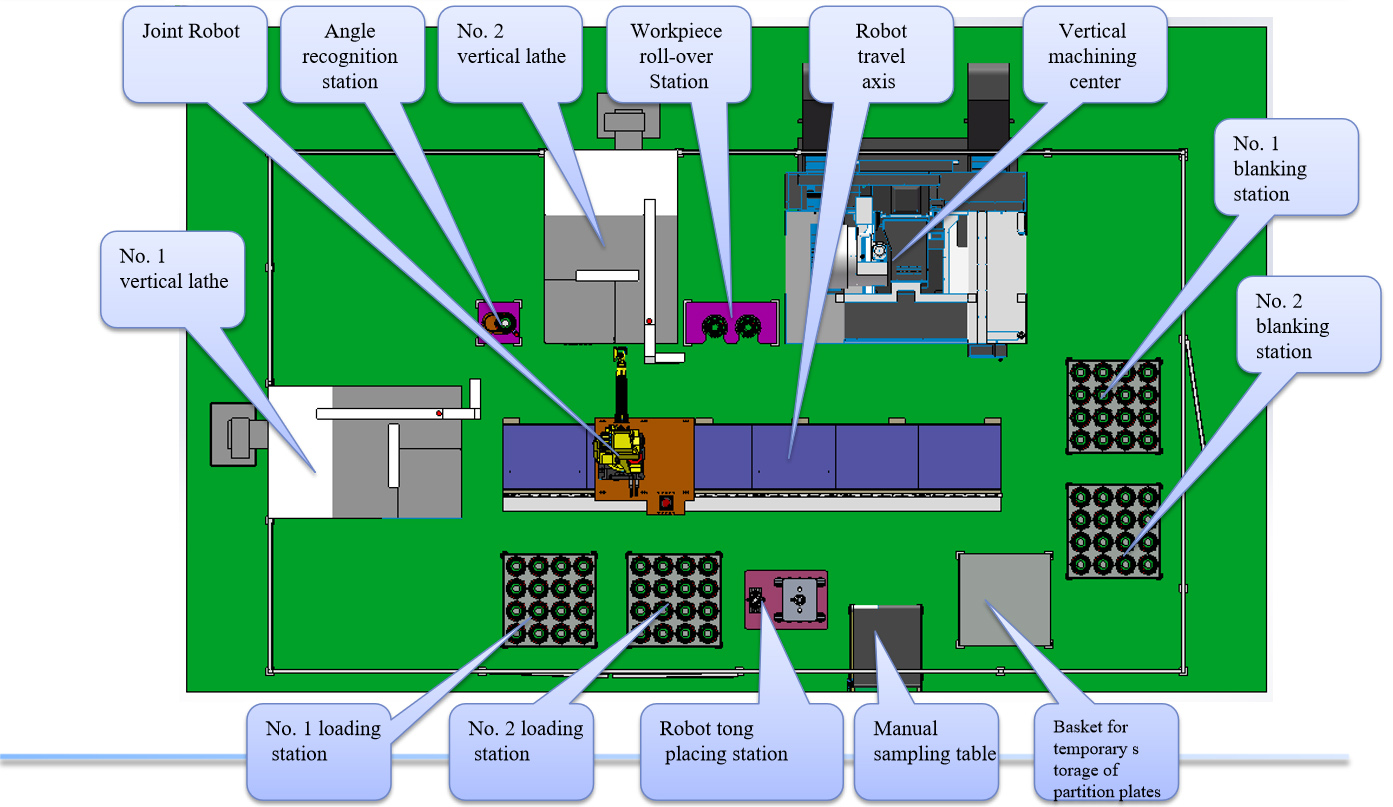
生產線主要功能部件介紹
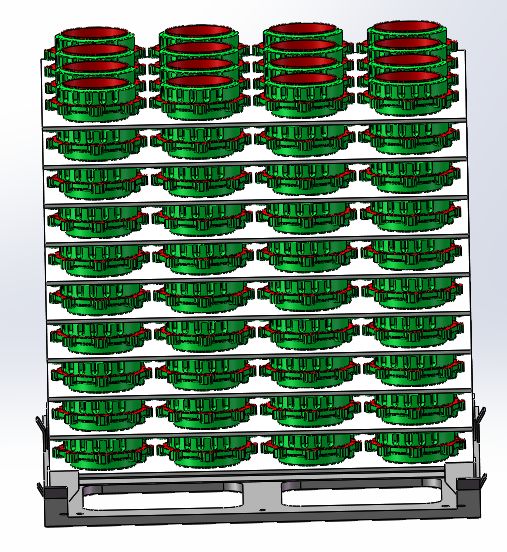
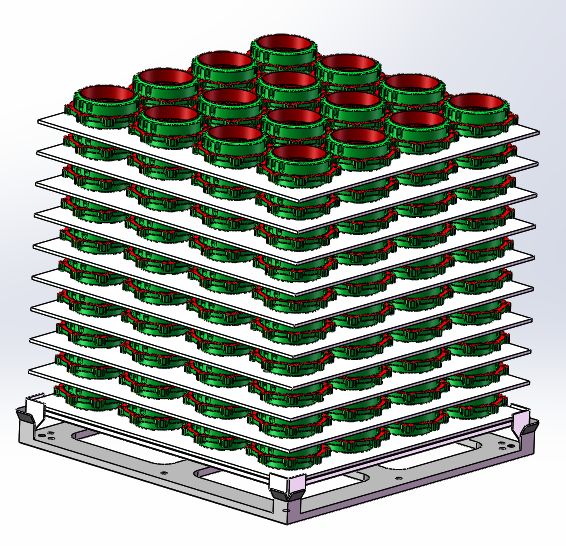
引入上下料系統
本方案自動化生產線存放設備為:堆疊托盤(每個托盤裝箱件數與客戶協商),提供工件毛坯3D圖或實物後確定工件在托盤中的定位。
1.工人將粗加工好的零件裝在料盤上(如圖),用堆高機搬運到指定位置;
2、堆高機更換托盤後,手動按鍵確認;
3.機器人抓取工件進行上料工作;
機器人行走軸介紹
該結構由關節機器人、伺服馬達驅動、齒輪齒條傳動組成,使機器人能夠進行往復直線運動,實現一台機器人服務多台機床、多工位抓取工件的功能,提高關節機器人的工作覆蓋率;
行走軌道採用鋼管焊接底座,採用伺服馬達、齒輪齒條傳動,增加關節機器人的工作覆蓋範圍,有效提升機器人的使用率;行走軌道安裝在地面上;
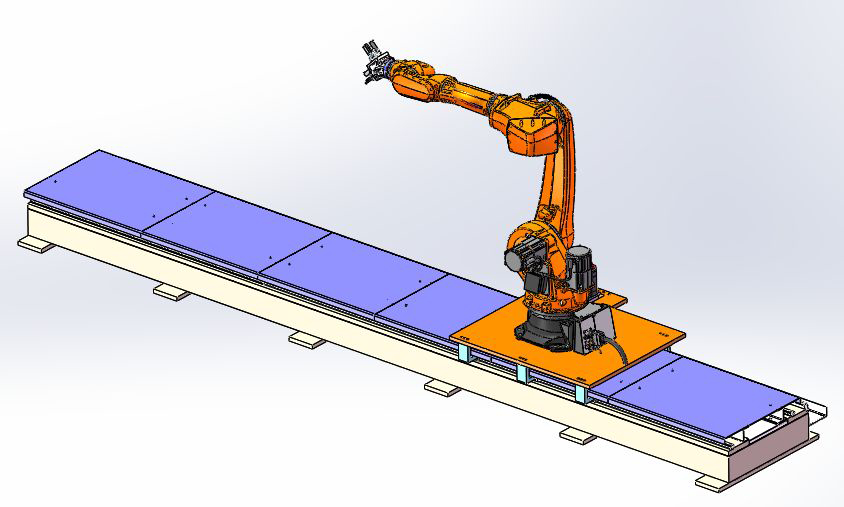
辰軒機器人:SDCX-RB500
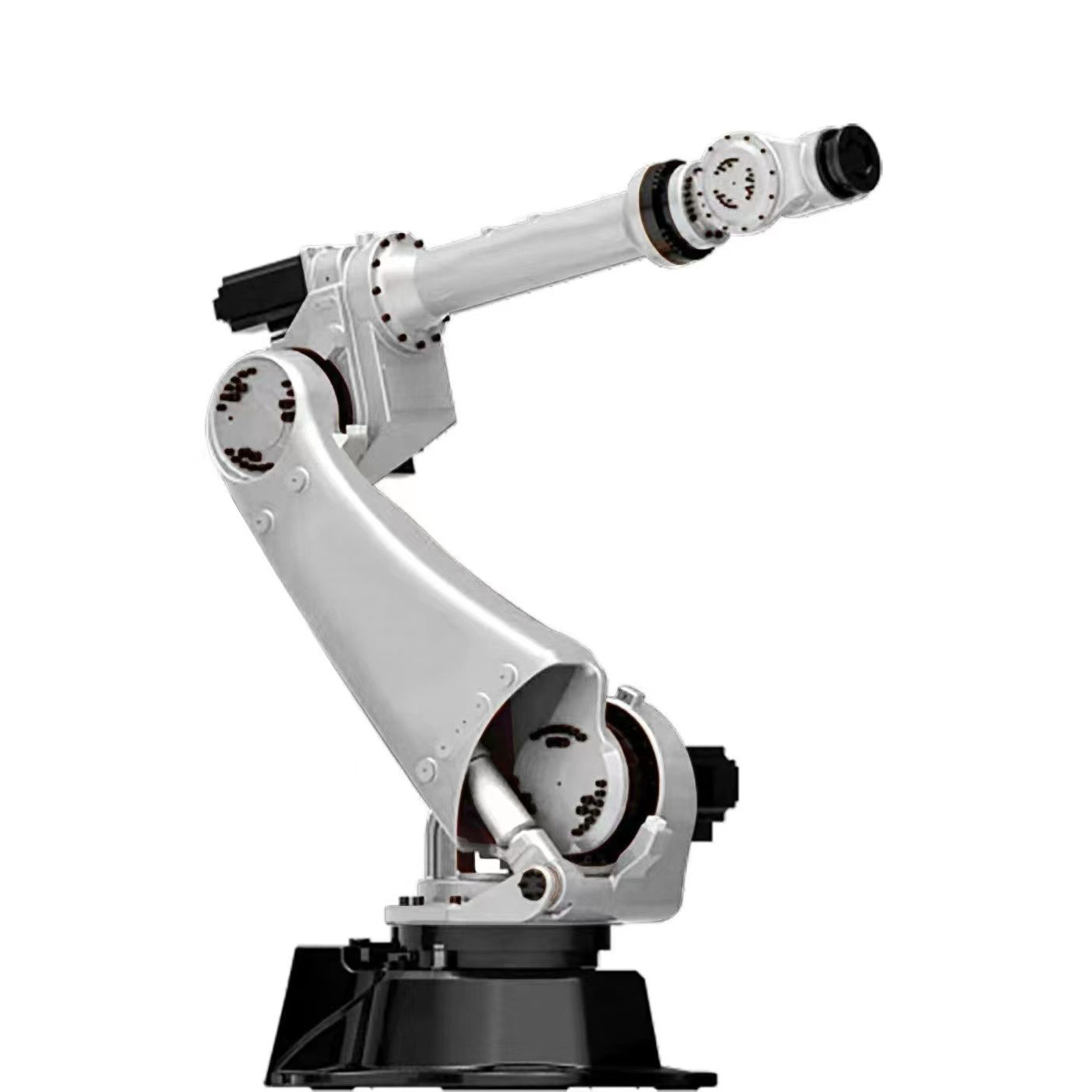
基本數據 | |
類型 | SDCX-RB500 |
軸數 | 6 |
最大覆蓋範圍 | 2101毫米 |
姿勢重複性(ISO 9283) | ±0.05毫米 |
重量 | 553公斤 |
機器人防護等級 | 防護等級,IP65 / IP67直列手腕(IEC 60529) |
安裝位置 | 天花板,讓傾斜角度≤0º |
表面處理、油漆 | 底座框架:黑色(RAL 9005) |
環境溫度 | |
手術 | 283 K 至 328 K(0 °C 至 +55 °C) |
儲存和運輸 | 233 K 至 333 K(-40 °C 至 +60 °C) |
機器人後部和底部擁有廣闊的運動範圍,可採用天花板升降安裝。由於機器人橫向寬度被壓縮到極限,因此可以緊密貼合相鄰的機器人、夾具或工件進行安裝。可從待機位置高速移動到作業位置,並在短距離移動中快速定位。
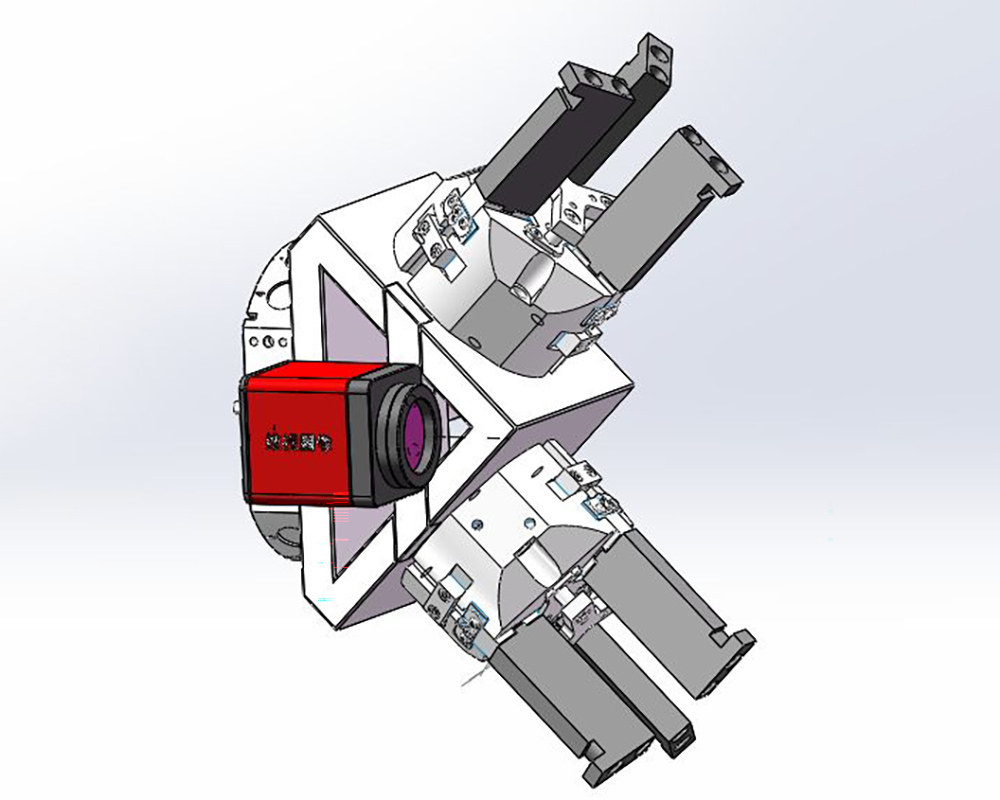
智慧機器人上下料鉗機構
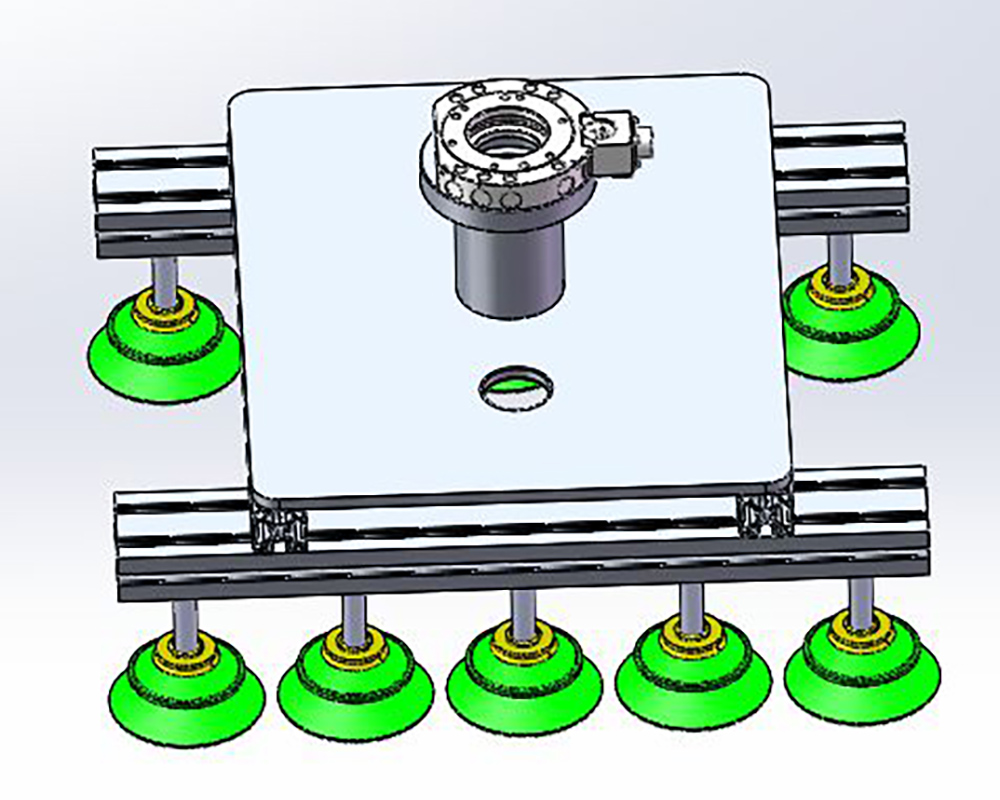
機器人隔板夾鉗機構
描述:
1.針對該零件的特點,採用三爪外支撐方式上下料,可實現該零件在機床上的快速車削;
2、機構設有位置偵測感測器及壓力感知器,檢測零件夾緊狀態及壓力是否正常;
3、機構設有加壓裝置,在停電、主氣路斷氣的情況下,工件不會在短時間內脫落;
4.採用手動換鉗裝置,更換夾鉗機構可快速完成不同材料的夾持。
換鉗裝置介紹
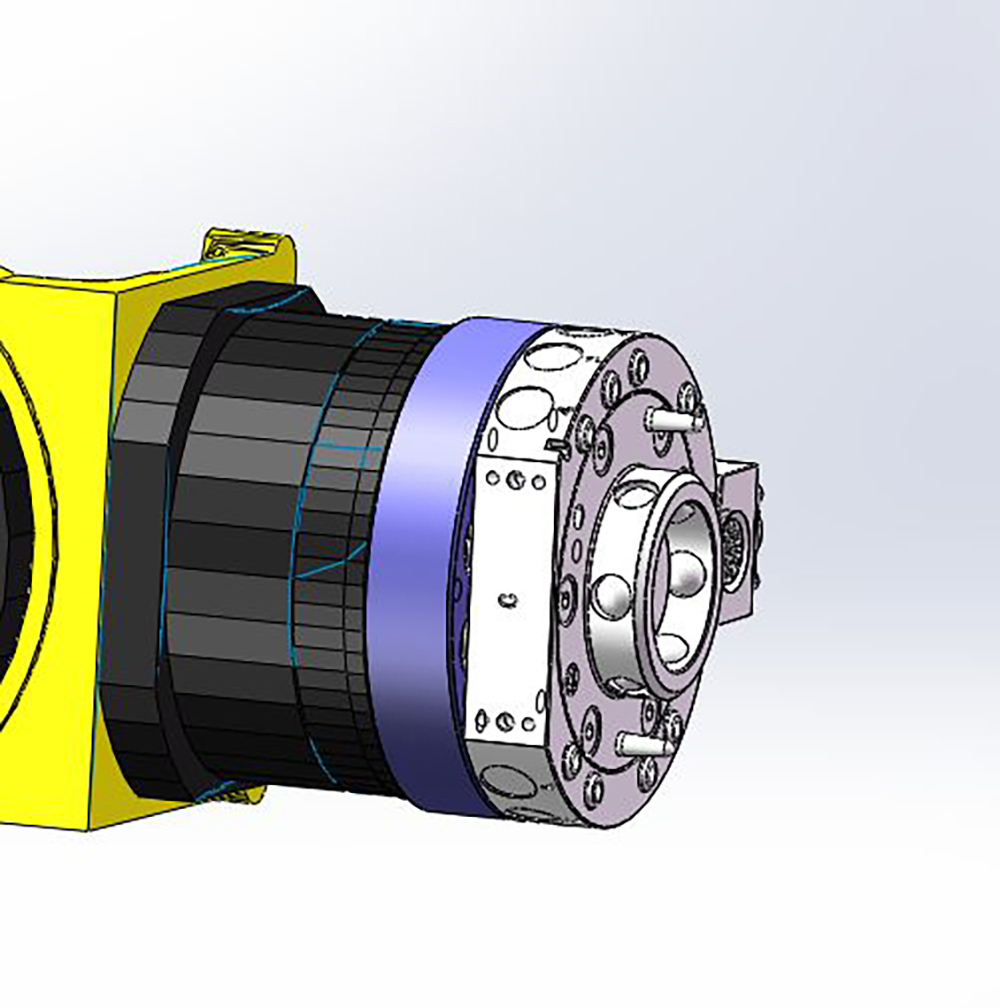
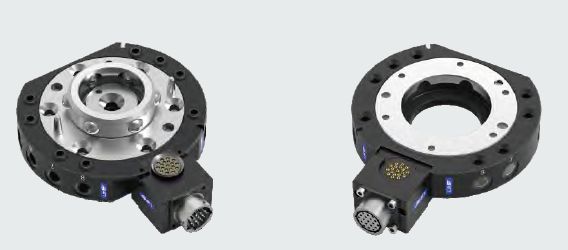
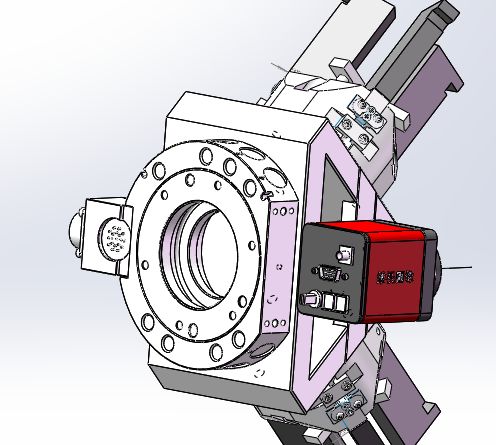
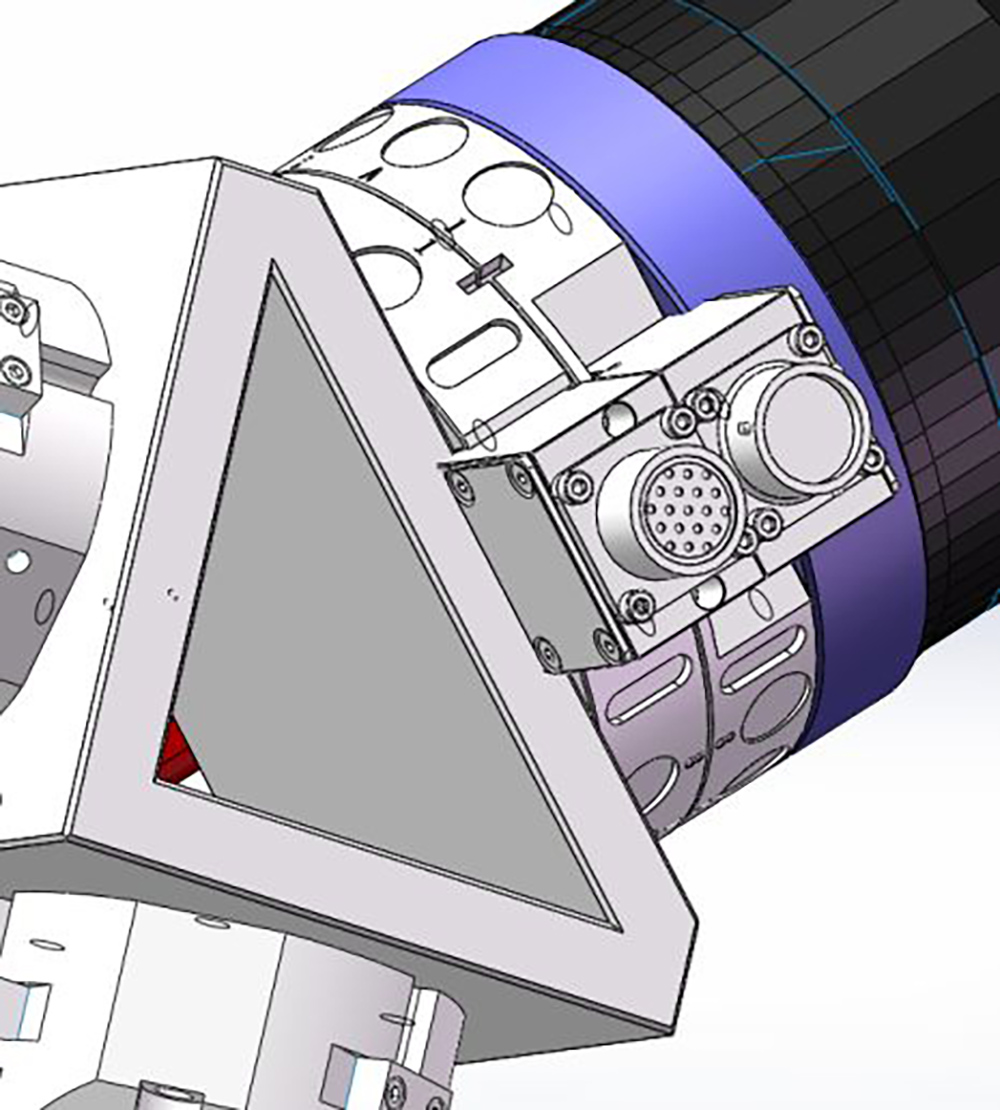
精密夾鉗更換裝置用於快速更換機器人夾鉗、工具端及其他執行機構。減少生產閒置時間,提高機器人彈性,其特點如下:
1.解鎖並擰緊氣壓;
2.可採用多種動力、液體、氣體模組;
3、標準配備可快速與氣源連接;
4.特設保險機構,可防止意外斷氣的風險;
5.無彈簧反作用力;6.適用於自動化領域;
視覺系統介紹-工業相機
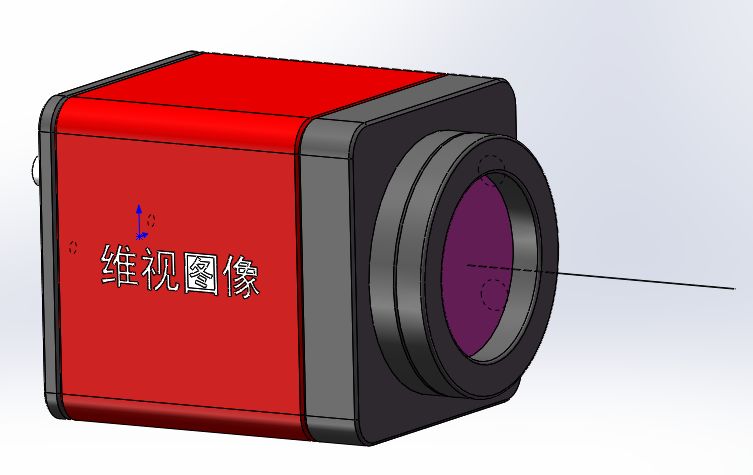
1.攝影機採用高品質CCD及CMDS晶片,具有高解析度、高靈敏度、高信頻比、寬動態範圍、成像品質優良、色彩還原能力一流的特性;
2.面陣相機有兩種資料傳輸方式:千兆乙太網路(GigE)介面、USB3.0介面;
3.相機結構緊湊,外型小巧,重量輕,安裝簡便。傳輸速度快,抗干擾能力強,輸出高品質影像穩定;適用於讀碼、缺陷偵測、DCR、圖案辨識等;彩色相機色彩還原能力強,適用於色彩辨識要求較高的場景;
角度自動辨識系統介紹
功能介紹
1.機器人從上料籃夾取工件,並送至轉盤定位區域;
2、轉盤在伺服馬達的驅動下旋轉;
3、視覺系統(工業相機)工作,辨識角度位置,轉台停止,確定所需角度位置;
4.機器人取出工件,放入另一件工件進行角度辨識;
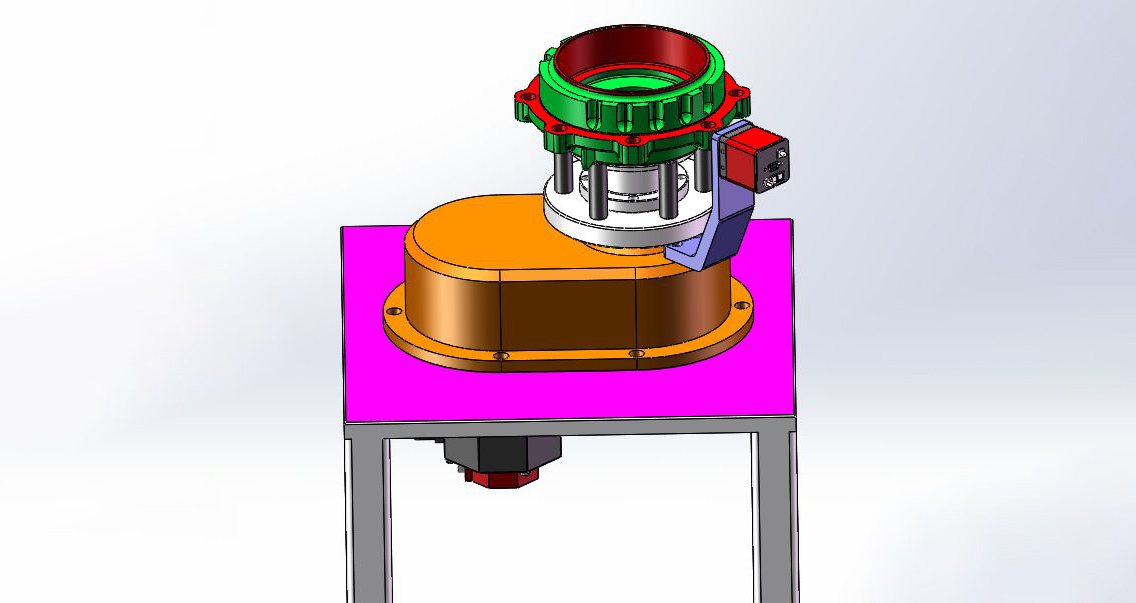
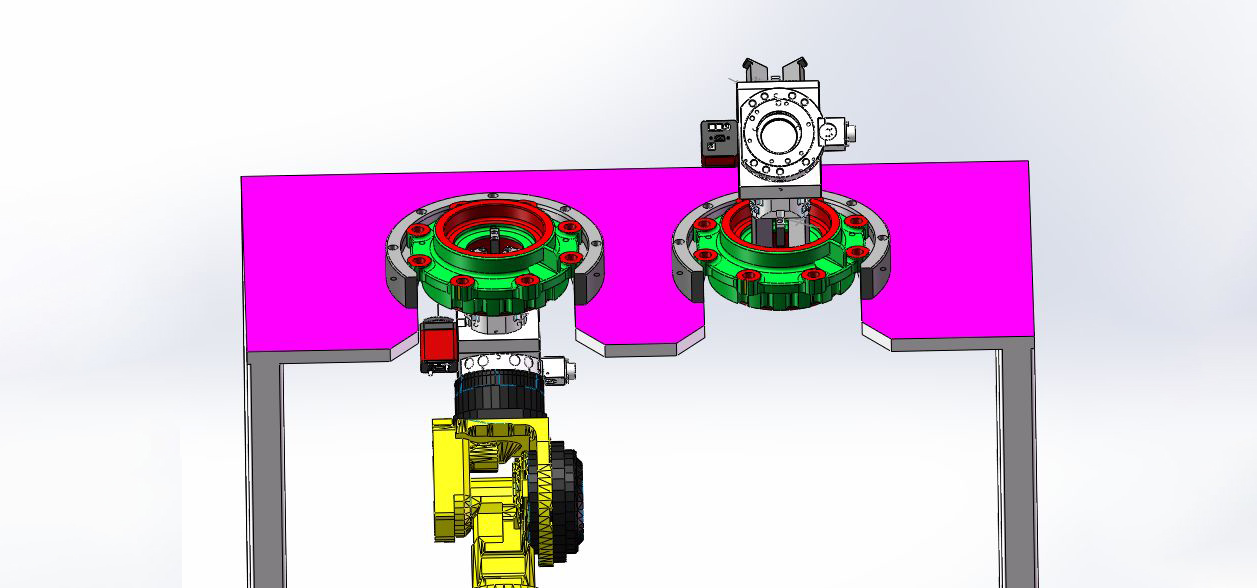
工件翻轉台簡介
翻車站:
1、機器人拿起工件,放置到翻轉台的定位區域(圖中左側工位);
2、機器人從上方抓取工件,實現工件的翻轉;
機器人夾鉗放置台
功能介紹
1、每層零件裝載完畢後,應將分層隔板放入隔板暫存籃內;
2、機器人可透過換鉗裝置快速更換吸盤鉗,並可拆除隔板;
3.隔板擺放好後,取下吸盤鉗,換上氣動鉗,繼續上料、下料;
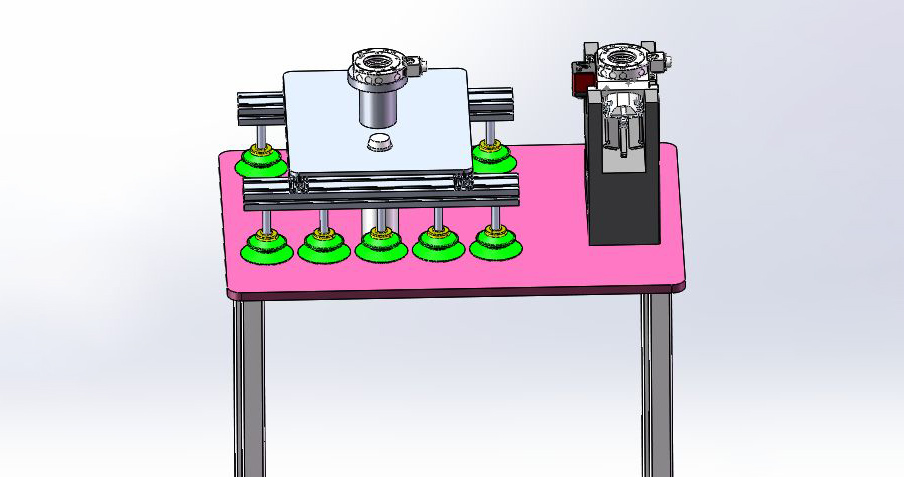
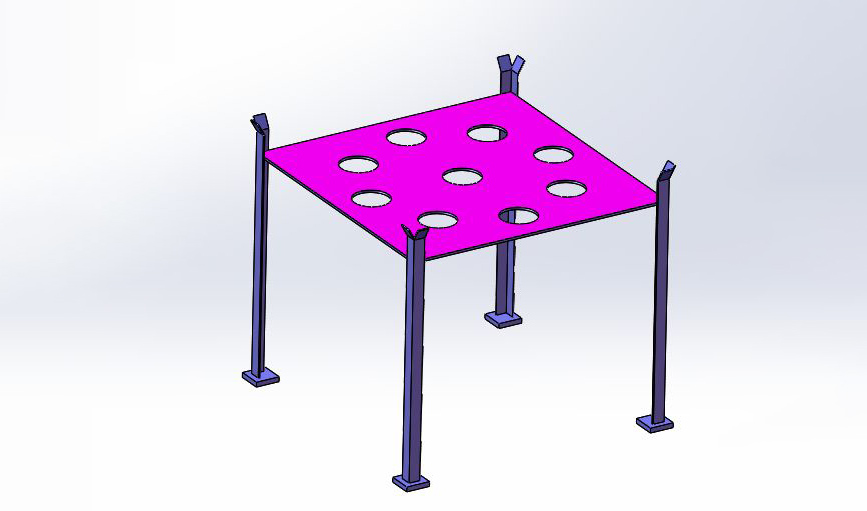
隔板臨時存放籃
功能介紹
1.設計規劃一個隔板臨時筐,先撤掉上料隔板,再使用下料隔板;
2.上車隔板人工擺放,一致性差,將隔板放入暫存籃後,機器人才能取出並整齊擺放;
手動採樣表
描述:
1、針對不同的生產階段設定不同的人工隨機取樣頻率,可有效監督線上測量的有效性;
2.使用說明:機械手依照手動設定的頻率將工件放置到採樣台的設定位置,並以紅燈提示。偵測人員按下按鈕將工件運送到防護外的安全區域,測量完畢後取出工件進行測量並單獨存放;
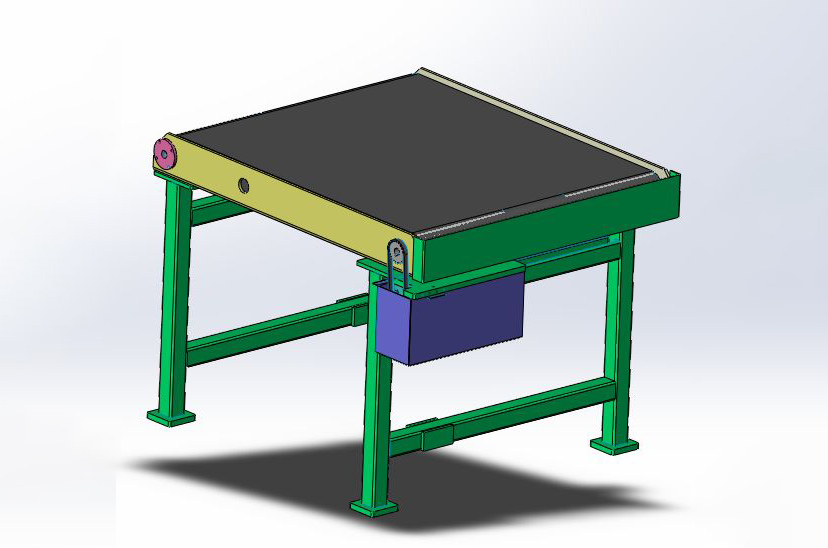
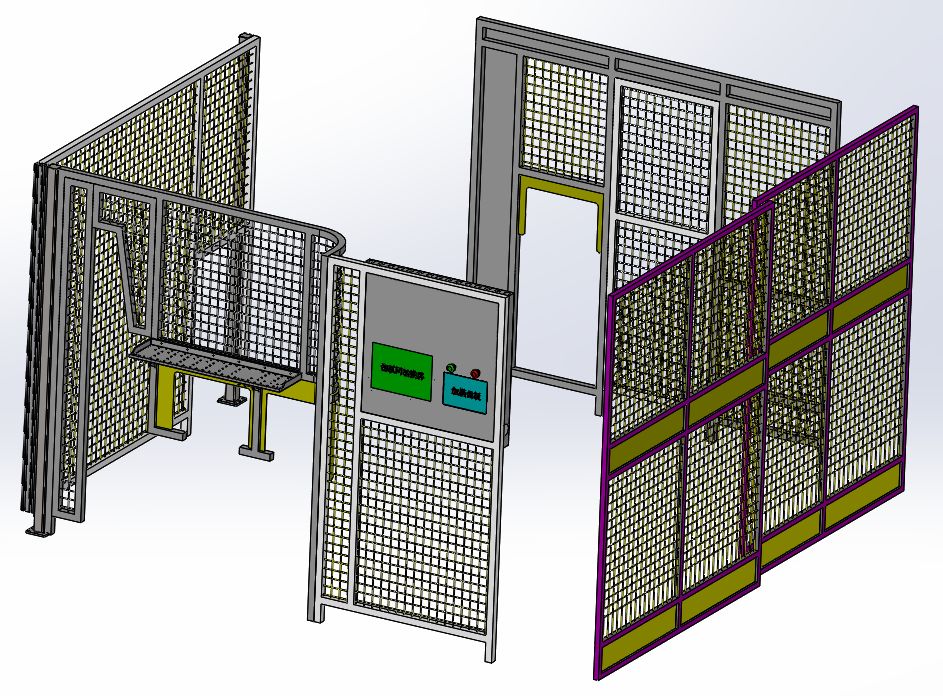
保護元件
採用輕量鋁型材(40×40)+網片(50×50)構成,觸控螢幕、急停按鈕可整合到防護部件上,集安全性與美觀於一體。
OP20液壓夾具介紹
處理說明:
1.以φ165內孔為基孔,以D基準為基面,以兩個安裝孔凸台外圓弧為角度限位;
2.透過工具機M指令控制壓板的鬆開、壓緊動作,完成安裝孔凸台上平面、8-φ17安裝孔及孔兩端的倒角加工;
3.夾具具有定位、自動夾緊、氣密性偵測、自動鬆開、自動頂出、自動沖屑、自動清潔定位基準面等功能;
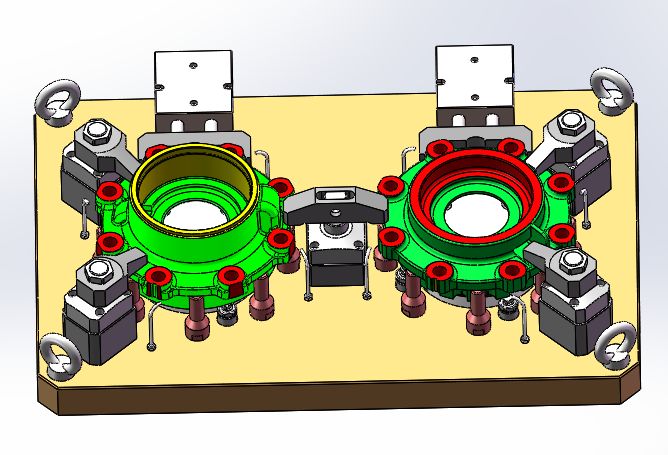
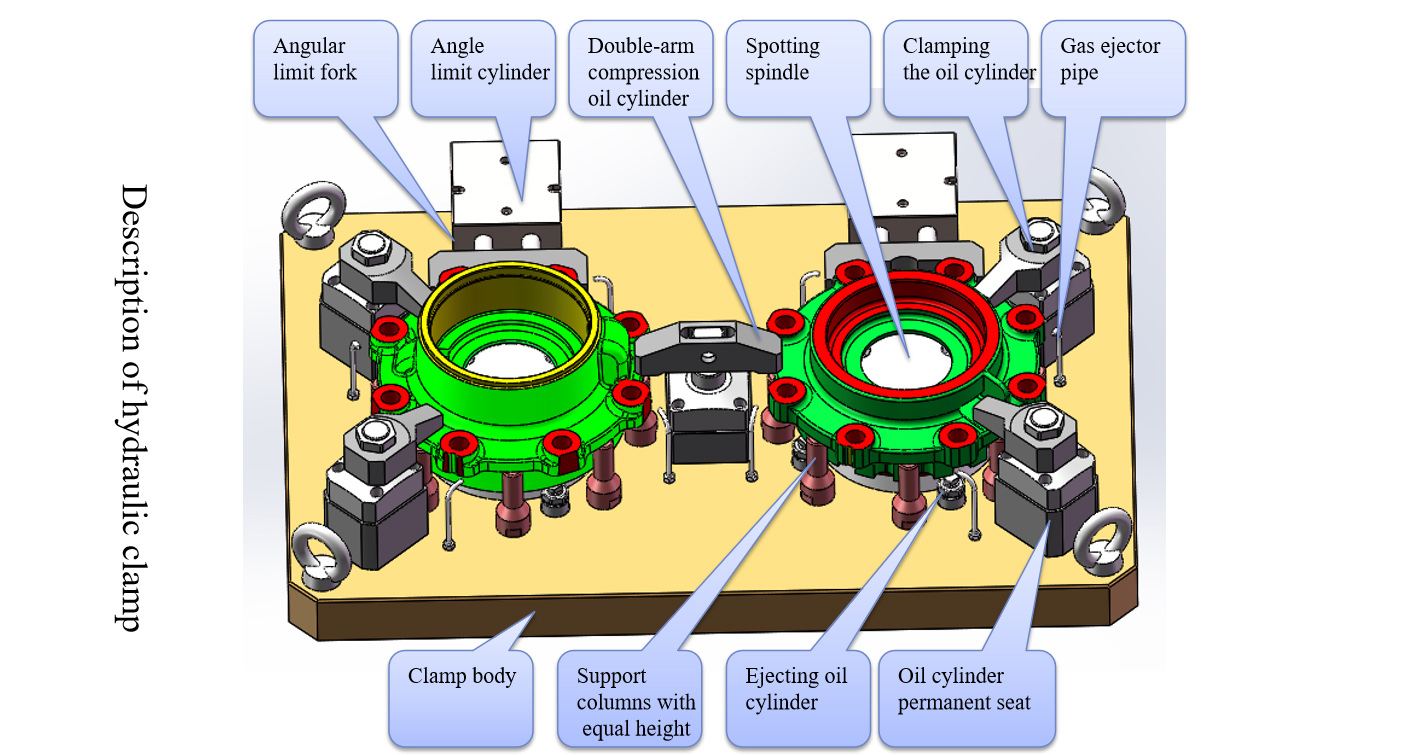
生產線設備要求
1.生產線設備夾具具備自動夾緊、鬆開功能,在機械手系統訊號的控制下,實現自動夾緊、鬆開功能,配合上下料動作;
2.生產線設備鈑金件需預留天窗位置或自動門模組,以配合我司電控訊號及機械手通訊;
3.產線設備透過重載連接器(或航空插頭)的連接方式與機械手通訊;
4.生產線設備內部(幹擾)空間大於機械手鉗口動作的安全範圍;
5.生產線設備應確保夾具定位面無殘留鐵屑,必要時應加大吹氣清理(清理時卡盤應旋轉);
6.生產線設備斷屑良好,必要時可增設本公司輔助高壓斷屑裝置;
7.當生產線設備要求工具機主軸準確停止時,增加此功能並提供相應電氣訊號;
立式車床VTC-W9035介紹
VTC-W9035數控立式車床適用於加工齒輪毛坯、法蘭、異形殼體等旋轉體零件,尤其適用於盤類、輪轂、煞車盤、泵體、閥體、殼體等零件的精密、省力、高效車削。工具機具有整體剛性好、精度高、單位時間金屬去除率大、精度保持性好、可靠性高、維護方便等優點,應用範圍廣泛,可實現流水線生產,效率高,成本低。
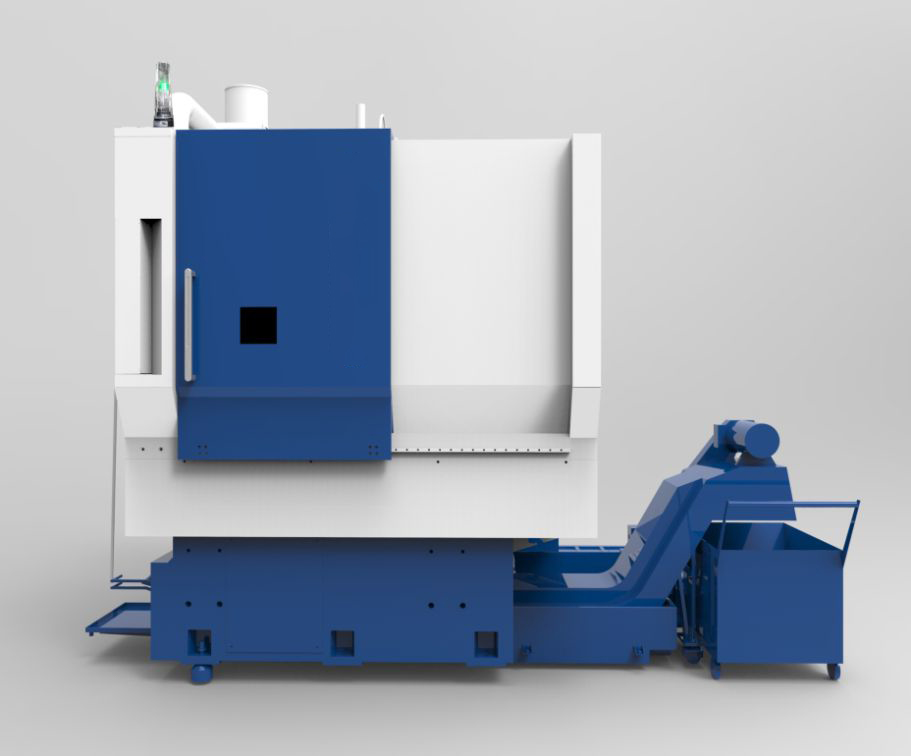
模型類型 | VTC-W9035 |
床身最大迴轉直徑 | φ900毫米 |
滑板最大迴轉直徑 | φ590毫米 |
工件最大迴轉直徑 | φ850毫米 |
工件最大車削長度 | 700毫米 |
主軸轉速範圍 | 20-900轉/分 |
系統 | FANUC 0i-TF |
X/Z軸最大行程 | 600/800 毫米 |
X/Z軸快速移動速度 | 20/20米/分鐘 |
工具機長、寬、高 | 3550*2200*3950毫米 |
專案 | 單元 | 範圍 | |
加工範圍 | X軸行程 | mm | 1100 |
X軸行程 | mm | 610 | |
X軸行程 | mm | 610 | |
主軸鼻端至工作台距離 | mm | 150~760 | |
工作台 | 工作台尺寸 | mm | 1200×600 |
工作台最大承重 | kg | 1000 | |
T型槽(尺寸×數量×間距) | mm | 18×5×100 | |
餵食 | X/Y/Z軸進給速度快 | 米/分鐘 | 36/36/24 |
主軸 | 駕駛模式 | 皮帶類型 | |
主軸錐度 | BT40 | ||
最大運轉速度 | 轉/分 | 8000 | |
功率(額定/最大值) | KW | 11/18.5 | |
扭力(額定/最大) | 牛·米 | 52.5/118 | |
準確性 | X/Y/Z軸定位精度(半閉環) | mm | 0.008(總長度) |
X/Y/Z軸重複精度(半閉環) | mm | 0.005(總長度) | |
刀庫 | 類型 | 光碟 | |
刀庫容量 | 24 | ||
最大刀具尺寸(全刀具直徑/空相鄰刀具直徑/長度) | mm | Φ78/Φ150/300 | |
最大刀具重量 | kg | 8 | |
各種各樣的 | 供氣壓力 | 百萬帕 | 0.65 |
電源容量 | 千伏安 | 25 | |
工具機外形尺寸(長×寬×高) | mm | 2900×2800×3200 | |
工具機重量 | kg | 7000 |
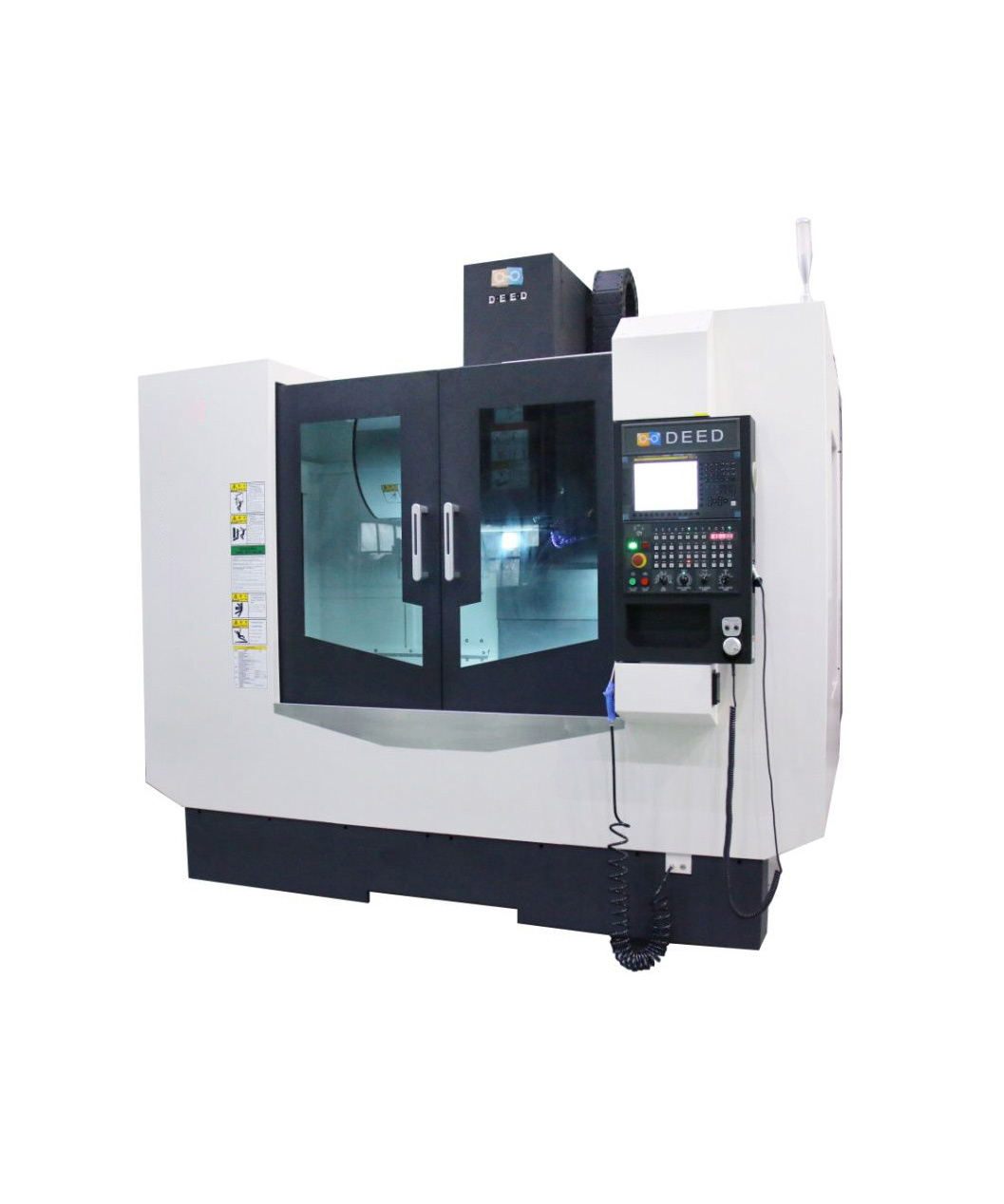